Sustainable Supply Chain Solutions Drive Gotham Greens Growth
Q&A With Gotham Greens CEO Viraj Puri
A substantial capital raise to continue its expansion, an acquisition, new plant-based dips … Gotham Greens has been making quite a few headlines in recent months. Indoor Ag-Con caught up with Co-Founder and CEO Viraj Puri to learn more about the company’s rapid growth and his drive to provide sustainable supply chain solutions to Gotham Greens’ diverse retail and foodservice customers.
Q: Gotham Greens recently raised an impressive $310 million in new capital. Can you share how you will/are using these funds to drive your company growth and mission?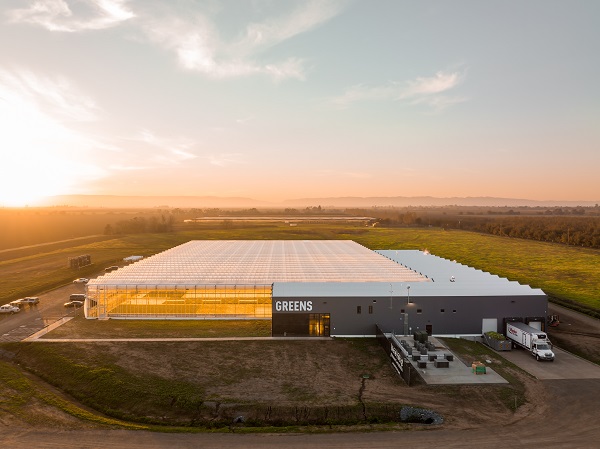
Yes, Gotham Greens recently raised over $310 million in new capital to accelerate our national greenhouse expansion. This new funding is key to advancing our greenhouse production capacity that will help us bring more fresh, local and sustainably grown greens to consumers across the country. We have new greenhouse projects actively underway in Texas, Georgia, and Colorado, as well as expansions at our existing facilities in Chicago and Providence. We also recently completed the acquisition of FresH2O Growers, Inc., a hydroponic greenhouse grower in Stevensburg, Va. (50 miles southwest of Washington, D.C.). By 2023, Gotham Greens will operate more than 40 acres (1.8 million square feet) of greenhouses across nine U.S. states: New York, Illinois, Rhode Island, Maryland, Virginia, Colorado, California, Texas, and Georgia.
Q: Indoor Ag-Con recently co-hosted the new CEA Summit East in Danville, Virginia. We were excited to see all the exciting CEA activity happening in/around the state, including your recently announced acquisition of Stevensburg, Virginia-based FresH2O Growers. What led to the decision to purchase this operation and what are your plans?
We are thrilled to welcome FresH2O to the Gotham Greens team. This acquisition provides additional production capacity for the East Coast. Gotham Greens and FresH2O share a desire to advance greenhouse agriculture and to bring more fresh, local and sustainably grown produce to consumers across the country, and we are confident we will continue to service FresH2O’s Mid-Atlantic customers with our high-quality, longer lasting leafy greens and other exciting innovations in the years to come.
Q: Tell us a little about Gotham’s new Plant-Based Dips. Why you decided to expand into this category and how it’s going?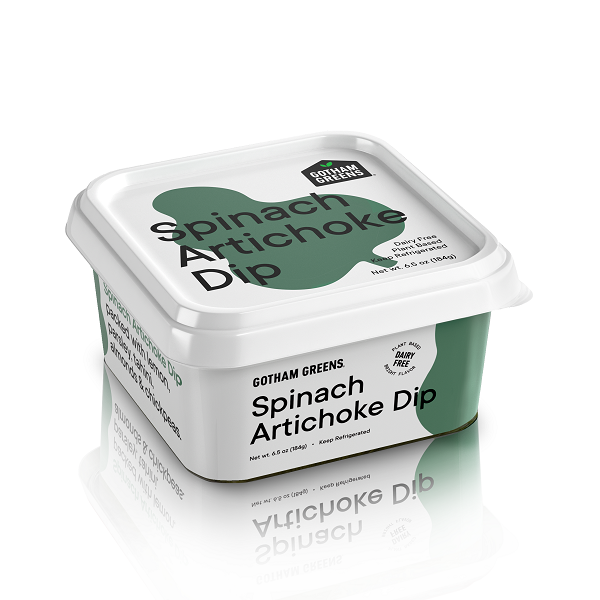
Gotham Greens is committed to bringing consumers the best-tasting, most flavorful fresh foods in the category. Our recent expansion into plant-based dips serves consumers in a brand-new way and speaks to cooking and dining trends we’ve seen over the past several years. Dips are one of the most well-loved snacks due to their versatility and craveable flavors, yet as consumers evolve their dietary habits to reflect a more plant-based and flexitarian lifestyle, the category has not kept up with bringing delicious plant-based options to market. We’re pleased with the response to date and are thrilled that they’re now available nationwide.
Q: Earlier this year you were one of 12 leaders appointed to the USDA’s new Federal Advisory Committee For Urban Agriculture. It’s probably early yet but can you share any insights on what the committee is working on to help promote/support urban ag across the country? 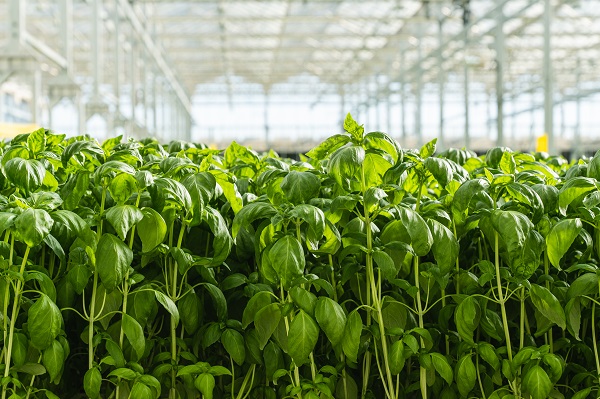
I’m honored to be part of this committee that aims to support urban agriculture, including issues of equity and food/nutrition access. As business leaders, we can make our products more accessible to more consumers across the country. In the case of Gotham Greens, we are aiming to do this by building enough scale and efficiency in our greenhouse operations that we can provide our products at a price parity to organic produce products.
The committee has been set up for various urban agriculture practitioners to develop recommendations and advise the USDA on policies, initiatives, and outreach that its new Office of Urban Agriculture and Innovation Production can hopefully put into practice. While these recommendations are still under development, I can say that they range from easing regulatory hurdles to helping to create sales channels for urban and innovative farmers.
One of the biggest factors influencing the ever-widening wealth gap is the cost of healthcare in this country. By providing more access to fresh, sustainably grown produce, we hope that consumers can follow a more balanced diet comprised of fresh vegetables and fruits for a healthier lifestyle. Now more than ever, we are committed to delivering high-quality, longer lasting, and nutrient-rich produce to people when it’s needed most. I believe it is essential to decentralize agricultural production and bring more greenhouse-grown produce and fresh, plant-based foods to people across the United States, and I look forward to continuing to work with the USDA to help further this cause.
Q: What’s next for Gotham Greens? 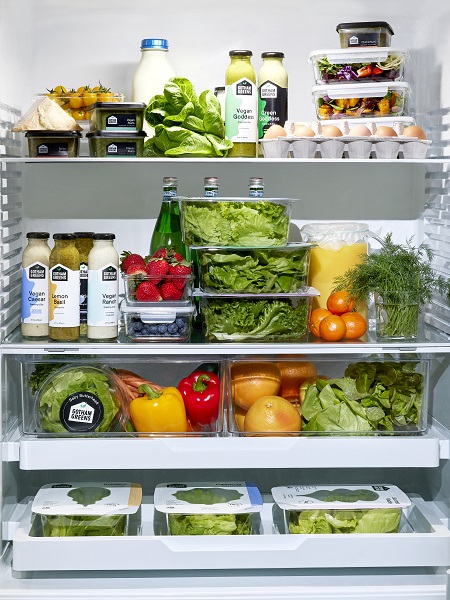
With increasing climate and supply chain related issues facing our food system, it’s more important than ever to bring innovative farming solutions that grow high-quality produce while using fewer precious natural resources. Gotham Greens is purposefully expanding its operations to provide sustainable supply chain solutions to its diverse retail and foodservice customers. The Colorado River is rapidly drying, creating a water crisis in seven states, including California and Arizona, which collectively provide 98% of leafy greens grown in the United States.
By using hydroponic growing systems in renewable electricity-powered greenhouses, Gotham Greens’ farms use up to 95% less water and 97% less land compared to conventional farming. The proximity of Gotham Greens’ greenhouses to key metropolitan markets also eliminates the need for long-distance refrigerated transportation while improving product quality and shelf life, and ultimately reducing food waste.
Gotham Greens is growing fast, and we look forward to bringing our brand to new markets in the coming months.
Learn more about Gotham Greens.